Finally got my intercooler heat exchangers. They are supposed to fit an early Mini Cooper and were only $55 each!! Yup, $110 for the pair new with a 1.3 bar pressure too. Also, two bosch water pumps that flow roughly 8gpm. Each turbo gets its own pump and heat exchanger. Way overkill for my boost levels, but, I really like the symmetry of each side identical and saved me from more plumbing to cross plumb both into one system.
Since the water/air intercoolers are now the top of the system, I had to come up with a way to fill and purge the air from the system. While puckered up abit drilling these holes in the intercooler end caps, I have one air escape hole, just remove the plug, and one fill hole that will go to a small motorcycle brake reservour that will attach to the side of the upright bars. Since there will be no pressure in the system, I can simply keep the reservour topped off and it will self purge any air.
Need to make the mounts for the he still, but I am amased at how much room I actually have left considering the complexity of the system as a whole. Lots of hours of staring at it coming up with a plan, but it is all coming together now in symmetry and cleanliness.
Since my side openings were already raised in height, I do not need to change that. But the blue tape marks how long I will need to cut out to expose the entire core to airflow. Not 100% set on the exact exterior design, but just happy I found a he that fits the parameters that works.
One more with plastic and flange completely drilled. I pulled a real dip shit move while tapping the very first hole in the flange. I usually put the tap in the drill and make easy work of it. Well, while doing the very first hole I said in my mind "whatever you do, do not break the tap off in the hole". Literally the second I completed that sentence in my head, the tap broke off in the hole. After 30 minutes trying to extract it, I just can't get it. It is harder than any drill bit, so drilling it out for a helicoil is ending up in dulled bits. I am afraid my last option is to cut the piece out, and weld it back up and grind smooth. Ugh. Tapped all of the rest by hand and it went smoothly.
Since the acrylic has a pretty high expansion rate with heat, I had to make the holes in the acrylic larger than the bolt size. A piece of foam will seal acrylic to the flange, and will have self sealing washers under head of bolts. Hoping this will be enough to keep from snapping bolts off. I will need to get fresh air running over the top of the acrylic to keep as cool as possible. Luckily, since it will never see vacuum in the plenum due to the itb's, I would only need to worry about boost pressure if the top becomes soft and wants to balloon. I also have some phenolic that is a great isolator from heat you can use as gaskets. Will need to get them water jetted out, but they are all the same and that should keep a little more heat out of the plenum.
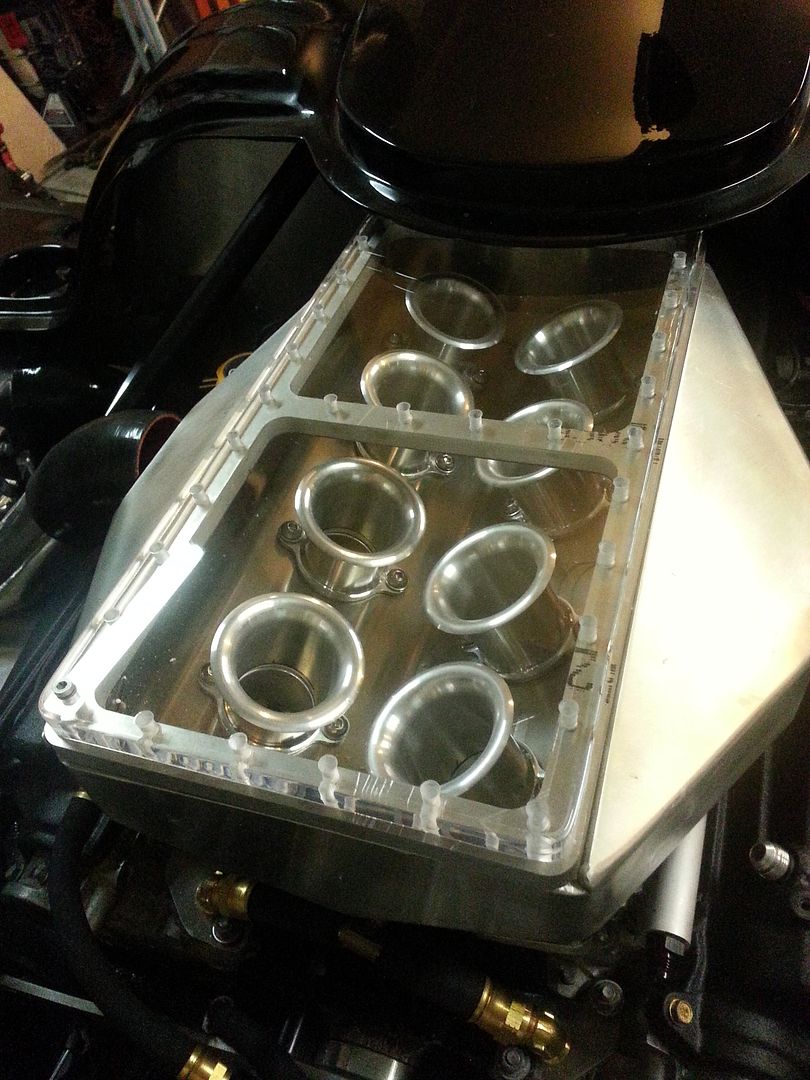