Hi all, a few updates
Mostly been fabricating little bits here and there from my big box of carbon fibre fabric offcuts and using up my left over epoxy resin before it goes out of date. The main new thing to share is the pedal box;
I need to swap out the accelerator pedal spring with a stiffer one when it arrives, but aside from that its done.
The pedal box will slide along the aluminium rails to adjust position. Ignore the white plastic bars, they are just temporary spacers i printed to hold the rails the correct spacing. The rails will be bonded and bolted to the tub floor.
I made the pedals and frame and footpads from the same process I have shown before .. print a two part mould on the 3D printer, chop up a load of carbon fibre into 50-100mm long strands, mix it with epoxy into the mould .. compress it all over getting all the mould filled (I jab it all over with wooden sticks, add a bit more fibre and resin, then jab some more). Then close the top of the mould and compress the whole thing tightly between clamps, let the excess resin bleed out. The mould needs to be printed quite strong to take the pressure.
my 3d printing booth / spare bedroom toilet, printing a mould for one of the pedals;
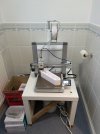
some photos before assembly;
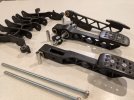
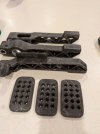
I've also been making a steering column and i'm about to start making a steering wheel. More on those in a future post !
Mostly been fabricating little bits here and there from my big box of carbon fibre fabric offcuts and using up my left over epoxy resin before it goes out of date. The main new thing to share is the pedal box;
I need to swap out the accelerator pedal spring with a stiffer one when it arrives, but aside from that its done.
The pedal box will slide along the aluminium rails to adjust position. Ignore the white plastic bars, they are just temporary spacers i printed to hold the rails the correct spacing. The rails will be bonded and bolted to the tub floor.
I made the pedals and frame and footpads from the same process I have shown before .. print a two part mould on the 3D printer, chop up a load of carbon fibre into 50-100mm long strands, mix it with epoxy into the mould .. compress it all over getting all the mould filled (I jab it all over with wooden sticks, add a bit more fibre and resin, then jab some more). Then close the top of the mould and compress the whole thing tightly between clamps, let the excess resin bleed out. The mould needs to be printed quite strong to take the pressure.
my 3d printing booth / spare bedroom toilet, printing a mould for one of the pedals;
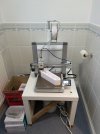
some photos before assembly;
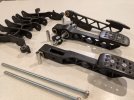
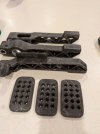
I've also been making a steering column and i'm about to start making a steering wheel. More on those in a future post !