Ron Earp
Admin
Stan Justus from Stallion Racing Components is doing a carb for the Lola Spider. He builds carbs for various racing applications, preparing both Holley and Demon carbs for whatever you might have in mind. He's building this carb based on the specifications of the motor that I provided him. He's given me permission to post the email and I thought I'd pass along this email from him.
Stan is a member here, and at Club Cobra, and is well-respected in race circles for his work. Seems to be very helpful on discussion of carbs, that is certain.
----
Hi Ron,
The following photos should give you an idea of where I’m at with your carb so far. The first pics are of the raw main body and metering block castings before any work. I very rarely buy complete carburetors to fill orders, preferring to start with un-machined castings which allow me to hold much tighter tolerances and also optimize many aspects of the finished carburetor (venturi minor diameter and entry radius, main circuit discharge nozzle size, shape, and position, etc.) to the customer’s exact requirements…or what his class rules require…or (ah hem) what the tech inspectors don’t know to look for. In your case, I started with the 1.375” venturi/1.687” throttle bore main body that is used on the Holley 750 HP Series four barrel carb, and raw Holley HP series metering block castings.
At this point, some machining has already been done to the blocks as I forgot to make sure that the memory card was in the camera the morning of the day I started on them.
The next pic doesn’t show a carburetor part at all, but is a photo of the fixture I use for the first machining operation on the main body. This is significant because it allows me to reference all machining operations from the true venturi X, Y, Z centerlines. Holley doesn’t concern themselves with this at all when machining these pieces; if the surface ends up “flat” and within oh… .050” and +/- 3 degrees of where the original engineering data calls for it to be, they assemble and ship it. That’s probably ok for someone’s street-stock oval tracker or 13-second bracket car, but falls well short of what our professional customers demand. Also, “squaring” the carb body properly means that I can put the part back on the same fixture later and make changes to the venture shape as small as .0005” without having to worry about tangency. This is a big deal if you are already “on” the maximum venturi diameter for a given class.
The main body mounts on the fixture like this.
The first cut is to the bottom surface to establish its distance from the vena cava (venturi choke point), and to drill the dowel holes that will be used to position the part on subsequent fixtures.
Next, the main body goes onto a fixture mounted on our 4th axis drive, which rotates to allow us to machine the sides and to drill and tap the various fuel and air passages for screw-in restrictions. These allow for easy tuning of the carburetor’s fuel response curve later. I also true the air-cleaner mounting surface, and radius the normally sharp and rough edges of the casting (carburetors should not draw blood when you touch them).
Next, the venturii are machined to the size and shape that matches the customer’s airflow/throttle response needs. This is done with a single-point tool, and the programs are quite long…the one written for your carb is 42,371 lines long. Thankfully, we have software that “reads” my 3-D drawings and writes the toolpath code for me…takes about a minute. I’ll see if I can copy some screen-shots of the actual process later.
The next pictures show the metering blocks being machined. The first operation (cutting the exterior profile) is mostly for appearance, but also gives me a consistent surface to work from, which everything that follows easier. Here, you see one of the idle circuits being profiled.
Here is the finish-machined metering block. Note that pretty much every metering orifice uses easily changeable screw-in restrictors. Our “baseline” calibrations are usually pretty close to optimum – provided the engine and application info supplied by the customer was accurate to begin with – but there are usually a few more lbs./ft. of torque to be had with some dyno-guided fine tuning. I’ll send “tuning supplies” along with your carb.
BTW – all of the zinc parts (carb main body, boosters, metering blocks, float bowls, etc.) will be dichromate plated for corrosion resistance once all of the machining and blending operations are done. This is basically the same process that Holley uses and results in the same gold/brown/greenish color, although we use a lot more chromium in our solutions so the surface is much more durable.
Machining/prepping the throttle shafts, butterflies, and baseplate itself will be next; I’ll send you some pictures of those operations as well…probably late next week. As for posting these pictures out on the site, feel free to do so if you think that the membership would like to see them.
----
I didn't know this much went into preparation for carb, pretty amazing. In the past I've used whatever carb I could get locally from a parts house, or minor race shop, which is basically stock for the most part. I thought maybe folks would like to have a look and I'll post the others if people are interested. I'm really excited to have Stan do the carb for me and looking forward to firing it up!
Best,
Ron
Stan is a member here, and at Club Cobra, and is well-respected in race circles for his work. Seems to be very helpful on discussion of carbs, that is certain.
----
Hi Ron,
The following photos should give you an idea of where I’m at with your carb so far. The first pics are of the raw main body and metering block castings before any work. I very rarely buy complete carburetors to fill orders, preferring to start with un-machined castings which allow me to hold much tighter tolerances and also optimize many aspects of the finished carburetor (venturi minor diameter and entry radius, main circuit discharge nozzle size, shape, and position, etc.) to the customer’s exact requirements…or what his class rules require…or (ah hem) what the tech inspectors don’t know to look for. In your case, I started with the 1.375” venturi/1.687” throttle bore main body that is used on the Holley 750 HP Series four barrel carb, and raw Holley HP series metering block castings.
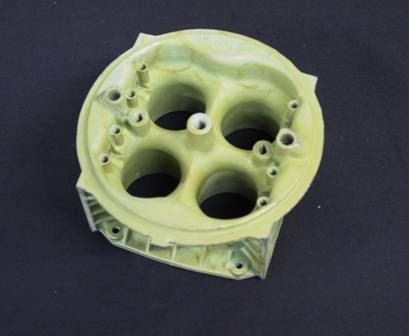
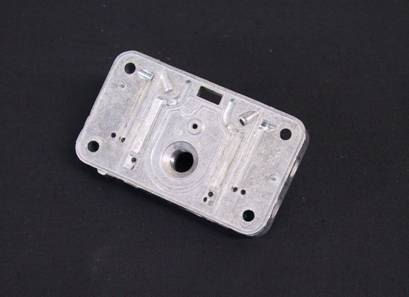
At this point, some machining has already been done to the blocks as I forgot to make sure that the memory card was in the camera the morning of the day I started on them.
The next pic doesn’t show a carburetor part at all, but is a photo of the fixture I use for the first machining operation on the main body. This is significant because it allows me to reference all machining operations from the true venturi X, Y, Z centerlines. Holley doesn’t concern themselves with this at all when machining these pieces; if the surface ends up “flat” and within oh… .050” and +/- 3 degrees of where the original engineering data calls for it to be, they assemble and ship it. That’s probably ok for someone’s street-stock oval tracker or 13-second bracket car, but falls well short of what our professional customers demand. Also, “squaring” the carb body properly means that I can put the part back on the same fixture later and make changes to the venture shape as small as .0005” without having to worry about tangency. This is a big deal if you are already “on” the maximum venturi diameter for a given class.
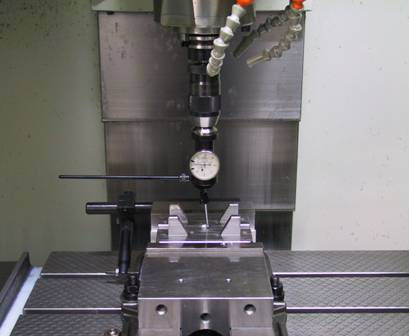
The main body mounts on the fixture like this.
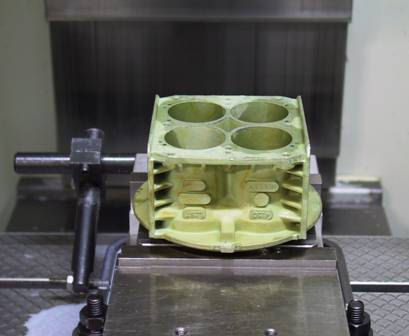
The first cut is to the bottom surface to establish its distance from the vena cava (venturi choke point), and to drill the dowel holes that will be used to position the part on subsequent fixtures.
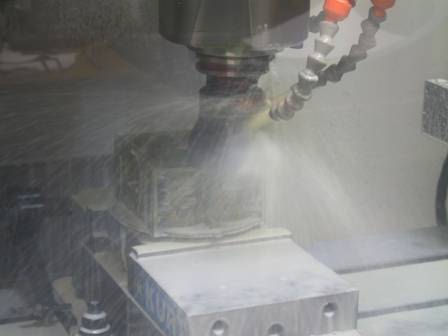
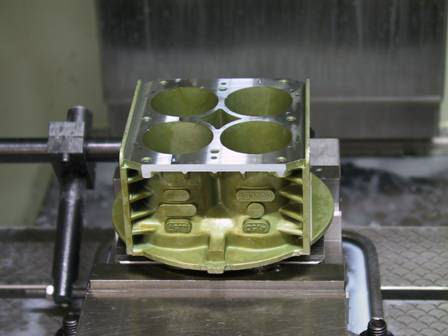
Next, the main body goes onto a fixture mounted on our 4th axis drive, which rotates to allow us to machine the sides and to drill and tap the various fuel and air passages for screw-in restrictions. These allow for easy tuning of the carburetor’s fuel response curve later. I also true the air-cleaner mounting surface, and radius the normally sharp and rough edges of the casting (carburetors should not draw blood when you touch them).
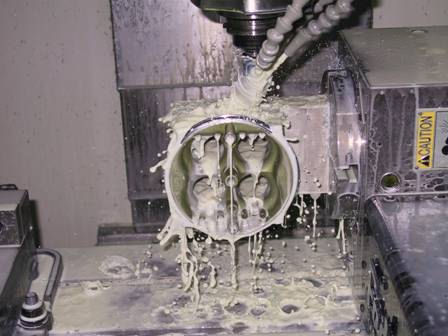
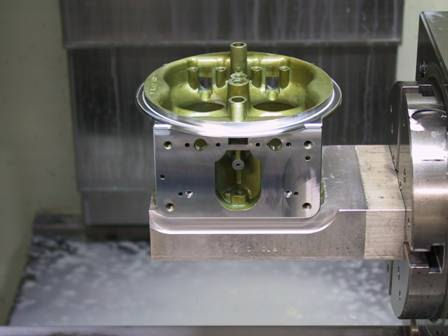
Next, the venturii are machined to the size and shape that matches the customer’s airflow/throttle response needs. This is done with a single-point tool, and the programs are quite long…the one written for your carb is 42,371 lines long. Thankfully, we have software that “reads” my 3-D drawings and writes the toolpath code for me…takes about a minute. I’ll see if I can copy some screen-shots of the actual process later.
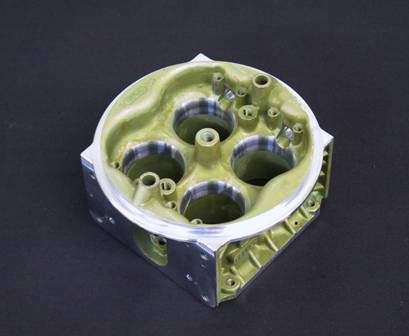
The next pictures show the metering blocks being machined. The first operation (cutting the exterior profile) is mostly for appearance, but also gives me a consistent surface to work from, which everything that follows easier. Here, you see one of the idle circuits being profiled.
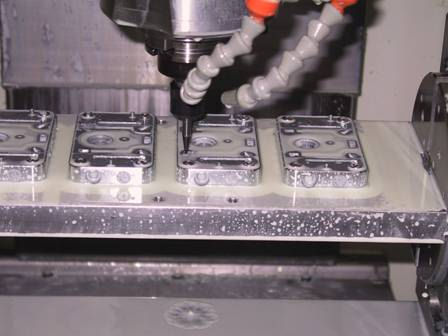
Here is the finish-machined metering block. Note that pretty much every metering orifice uses easily changeable screw-in restrictors. Our “baseline” calibrations are usually pretty close to optimum – provided the engine and application info supplied by the customer was accurate to begin with – but there are usually a few more lbs./ft. of torque to be had with some dyno-guided fine tuning. I’ll send “tuning supplies” along with your carb.
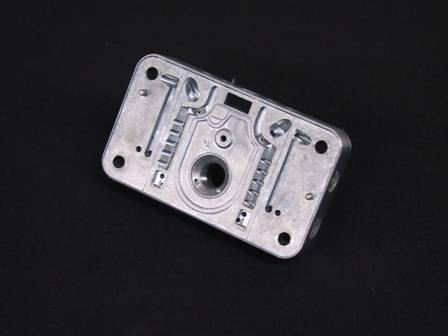
BTW – all of the zinc parts (carb main body, boosters, metering blocks, float bowls, etc.) will be dichromate plated for corrosion resistance once all of the machining and blending operations are done. This is basically the same process that Holley uses and results in the same gold/brown/greenish color, although we use a lot more chromium in our solutions so the surface is much more durable.
Machining/prepping the throttle shafts, butterflies, and baseplate itself will be next; I’ll send you some pictures of those operations as well…probably late next week. As for posting these pictures out on the site, feel free to do so if you think that the membership would like to see them.
----
I didn't know this much went into preparation for carb, pretty amazing. In the past I've used whatever carb I could get locally from a parts house, or minor race shop, which is basically stock for the most part. I thought maybe folks would like to have a look and I'll post the others if people are interested. I'm really excited to have Stan do the carb for me and looking forward to firing it up!
Best,
Ron